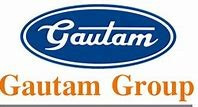
Gautam Technocast Solves Costly Leakage Issues with Simulation-Driven Gating & Risering Optimization using ESI QuikCAST
Gautam Technocast
Established in 1962, Gautam Technocast supplies a wide range of parts, including housings, front axle parts, 4WD drive axle parts, and counterweights to original equipment manufacturers (OEMs) in the tractor, automotive, and engineering industries.
The Challenge for Gautam Technocast
Gautam Technocast faced a recurring issue with casting leakage in the speed housing, a critical component in tractor transmissions. The problem was identified during final assembly and leak testing, after the parts had been machined. As a supplier of raw castings to M/s CAPL, Gautam Technocast was unable to detect the leakage defect before machining, leading to the rejection of entire transmission assemblies. This problem caused significant losses for their customer, as defective assemblies were only discovered at the customer’s end.
The root cause of the defect was inadequate metal feeding during the melting and pouring process, leading to shrinkage at the heavy section of the part. The shrinkage defect would open after machining, causing leaks that compromised the quality of the final product.
Why use Casting Simulation Software as a Solution?
The decision was made to use simulation software to try and solve the leakage problem as would reduce and shorten the lead time for development while minimizing manufacturing risks. It enables correct and faster decision-making without the need for actual casting trials, and it provides a better understanding of the factors responsible for defects.
Why Choose QuikCAST from ESI?
QuikCAST was chosen as the software to run the simulations because it is a reliable and cost-effective tool for casting design optimization, prediction of part quality, and overall process improvement. It is an easy-to-use software that covers a wide range of casting processes and alloy systems, and shows good correlation between simulation and shop floor results during the evaluation stage. Additionally, QuikCAST has a good reputation and existing user base across similar organizations, offering a level of reassurance to Gautam.
How QuikCAST Solved the Problem
Using QuikCAST, Gautam Technocast was able to identify the exact location of the shrinkage defect caused by delayed solidification. The simulation provided a clear understanding of the inadequate metal feeding process and pinpointed the source of the issue.
As seen in the images, the solidification pattern is showing isolated liquid pockets /hotspots at the heavy section, which are ending up as shrinkage porosity. These open during machining and connect with tapping holes resulting in leakage issue.
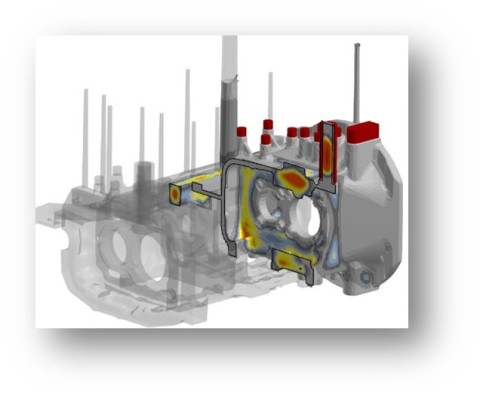
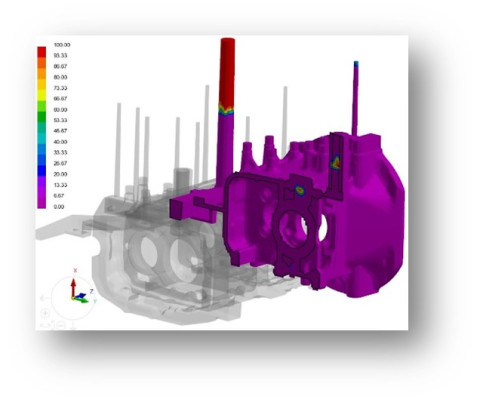
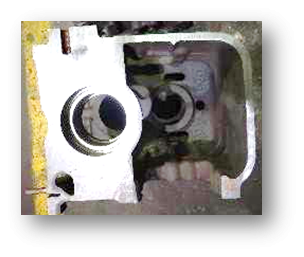
The Outcome
As a result of the identified issue in QuikCAST, a corrective action was implemented to address the shrinkage defect by adding an ND3 sleeve riser at the defect-prone location. This modification was optimized according to part geometry and modulus requirements for better feeding.
Following these changes, simulations confirmed that no defects remained, and subsequent testing at the customer’s facility verified that the corrective measures were successful. The problem was resolved with no additional costs incurred by the customer.
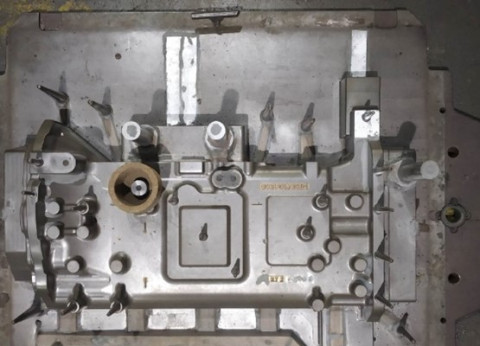
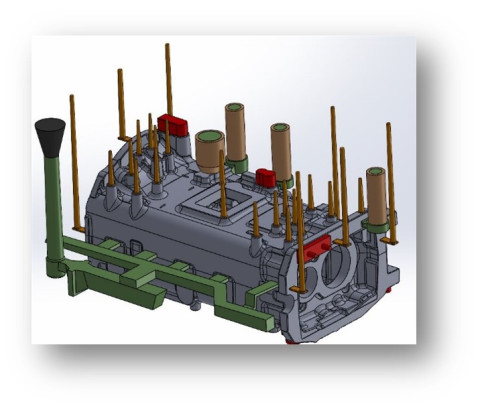
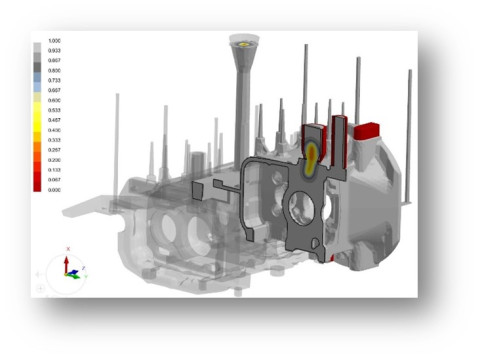
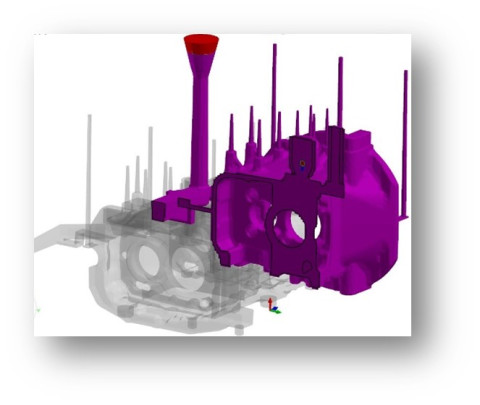
The Return on Investment (ROI) for Gautam Technocast
The implementation of QuikCAST and the corrective actions provided the following significant benefits for Gautam:
Zero customer complaints: The recurring leakage issue was eliminated, leading to greater customer satisfaction.
Reduced losses: The average rejection of 3 tractor transmission assemblies per month was eliminated.
Cost savings: Gautam Technocast saved approximately 8,000 INR per rejected part, while also reducing overall rejections and eliminating segregation activities at the customer’s end.
Increased customer confidence: The resolution of this chronic issue increased the customer’s trust in Gautam Technocast’s team.
Reduction in Cost of Poor Quality (COPQ): Overall quality and efficiency improved, reducing costs related to defective products.
By leveraging QuikCAST’s simulation capabilities, Gautam Technocast was able to enhance its manufacturing process, eliminate a chronic defect, and strengthen its relationship with key customers
ESI worked with icube Engineering Solutions to bring QuikCAST to Gautam Technocast. iCube Engineering Solutions, a specialist Engineering consulting firm provides solutions around Engineering Design, New Product Design, Casting simulation, Forging simulation, Revers Engineering, Product photo render, Casting part Gating design, Forging component development and 2D drafting services. We deliver reliable & scalable technology for digital transformation and have always been a top solution & service provider to our clients thereby improving their efficiency, design process & standardization. https://icubeengineering.in/