PROSIVIC
Manufacturers are continually improving autonomous vehicles with the goal of safely reaching Level 2 autonomy. To achieve that level of safety, departments within OEMs and Tier 1 suppliers who are responsible for evaluating the performance of their sensing software and sensors integrated into the vehicle, must measure how the sensing and intelligence would operate in every required driving situation. But how do they achieve that without having to drive billions of miles of open road tests?
Optimizing safety requires that sensors be integrated into the vehicle. In turn, artificial intelligence (AI) software relies on these sensors for information related to object detection & tracking, path planning, and driving tasks. When sensors lack performance, the phenomena initiates a trickledown effect, ultimately impacting AI performance. Hence the necessity for suppliers of complete assistance systems to simulate sensors with a high level of fidelity, and to run virtual test drives that are highly realistic.
For many, NCAP for Safety Assist is a major selling point and sets performance requirements for the vehicle intelligence systems – this includes sensing performance requirements. Unfortunately, with each new NCAP update, tests increase in number and complexity, requiring tens or even hundreds of driven tests. This makes preparation for NCAP more costly for OEMs and Tier 1 suppliers.
These challenges only scratch the surface of why Virtual Prototyping is indispensable.
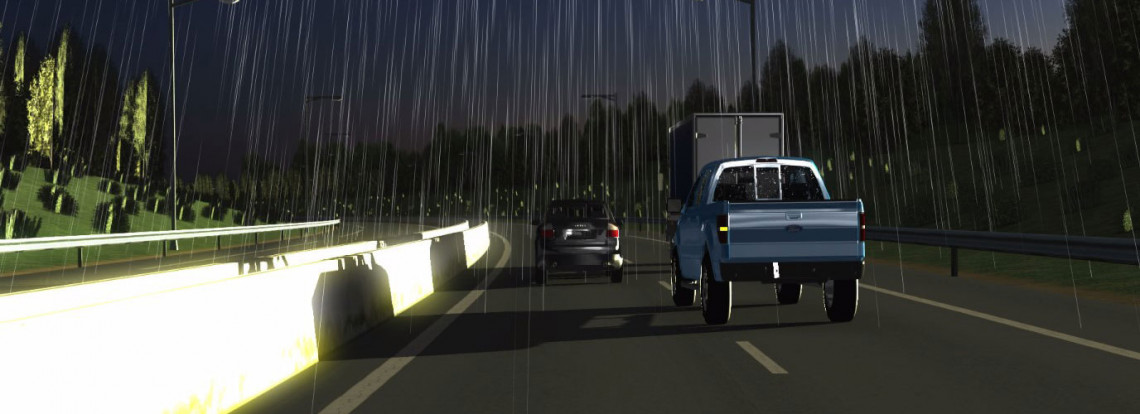
ESI PROSIVIC simulation software offers repeatable tests, access to high-value, real-life driving situations, and full control over simulations, all with zero real prototypes. Additionally, you gain flexibility and scalability for testing, shorter iteration cycles during development, and increased confidence in safety assessments.
Besides simulating vehicle dynamics and traffic situations for decision-making, function performance analysis requires specific simulations of the quality of the sensing data.
PROSIVIC assists with the preparation and execution of such simulations with a straightforward workflow. Users can design their own scenarios using built-in or imported data and create scenario variants of interest for the necessary parametric studies. The sensor hardware characteristics, the mounting settings, and the host vehicle attributes can be modeled. The PROSIVIC platform is open and connects to other simulation tools necessary to simulate certain subsystems (such as sensor fusion or situation analysis, vehicle control, or behavior models). For each evaluation, the data to be monitored and recorded can be adjusted to facilitate results diagnostic as post-processing. Finally, the simulations can be run in a manual or automated way.
Benefits of ESI PROSIVIC
- Work with the GUI or use scripting (such as python) allowing for more flexibility to scale from studying specific use cases to preparing extensive performance verification
- Access to high-fidelity sensor models complemented by rich virtual scene content that come with all the required physics for sensor simulations
- Ease integration through co-simulation with the user’s environments using protocols and standards such as OMG DDS and FMI
- Make crucial design decisions about sensor choice, positioning, and configuration early in the system development cycle
- Verify & validate the development of intelligence software on a continuous basis
- Enhance system performance by assessing nominal to critical environment conditions for vehicle sensing
- Reduce the amount of testing, improving the quality of early deliveries to customers
- Explore technical possibilities from future systems in a fully virtual environment
We were looking for a Virtual Prototyping software with the ability to develop physics-based sensor models. We wanted to integrate this feature within our own existing open-sourced engine. The perfect fit for us, with the answer to our problem, was ESI.
Xiaosong YangSenior Architect / Project Vice-Director, GAC R&D Center, Silicon Valley
Virtual Test Data Creation with High-Fidelity Sensing Simulation
ESI PROSIVIC sensor models cover the entire range of hardware equipment available on the market through parametrization. Connected to the user’s sensing processing software, they deliver high-fidelity simulation of sensing data. The parametric approach – for the scene, the behavior of road users, the weather, and sky conditions – provides the freedom to go from common case simulation to the corner cases, which are most challenging for individual sensors.
Key Benefits
- Configurable models of camera, radar, and lidar: 24-77GHz radar, optical camera, and near-infrared laser models
- Access scene libraries with object physics properties for sensors
- Obtain data to measure the in-vehicle performance of the sensing, in operational conditions, and before data from physical tests
- Gather reliable comparison data to benchmark different possible sensing options
- The virtual databases of scenarios improve testing flexibility towards sensing requirement changes during projects and reduces costs of future projects
- Run early, high-fidelity simulations and refine the performance KPIs for the sensing system
Easy Integration of Sensing into Existing Simulation Toolchains
Interfacing is usually perceived as complex and time-consuming – but with PROSIVIC it is as simple as ever. We specifically designed it so that it integrates easily into any software toolchain. PROSIVIC can exchange simulation data – including sensor outputs and the dynamic ground truth from the virtual scenarios – for processing from any other software. It also supports actuation feedback on PROSIVIC dynamic vehicles which enables closed-loop simulation. Additionally, it integrates with test automation processes involving scripting and remote execution control.
Key Benefits:
- Reuse existing simulation infrastructure and tools used by other departments; no toolchain migration necessary
- Gain access to sample interface components from other popular software providers
- Extend API independent of a tool vendor to connect new software. Gain access to source code, tutorials, and examples
- Co-simulation with other simulation tools is easy and straightforward, reducing extra simulation costs
- Integrate PROSIVIC with an automation flow using the remote-control API
Virtual Verification for Preparation of Function Assessment EURO NCAP Testing
PROSIVIC is committed to delivering the highest possible sensor modeling fidelity, which is necessary to prepare for virtual certification. Virtually create assessment tests and measure the sensing performance of the test conditions. The tool flexibility gives you full control over test conditions, such as variants of standardized test conditions or even custom proving ground tests – all decided by the user. After real test runs are carried out, data from real test logs are used to reproduce actual vehicle motions and simplify the understanding of system failures in real test campaigns.
Key Benefits
- Obtain high-fidelity test data (sensing and diagnostic information) with the correct sensors, before the prototype vehicle and equipment hardware have been developed and tested
- Measure the difference between sensing architecture choices (Ex. current vs. new generation of sensors on a vehicle)
- Improve confidence and communication on functionality performance by extending the test scenarios and conditions to cover your own set of proving ground tests
- Reduce the needed number of real tests and the costs related to them
- Capitalize on virtual test databases related to certification across vehicle programs, keeping the knowledge in-house and improving company expertise with difficult situations
- Share virtual databases between development function actors, improving consistency of performance comparisons and trust throughout the testing process