PAM-STAMP
Simulating Advanced and Flexible Sheet Metal Forming Processes with PAM-STAMP
Complementing the recently released automotive-specific BM-Stamp Stamping Simulation software, PAM-STAMP is a trusted sheet metal forming solution with over 25 years of proven use across aerospace, white goods, heavy machinery, and electronics industries. The solution includes a high degree of flexibility which allows to tackle sheet metal formability challenges across advanced and flexible processes—all within a single environment. From part and tooling design phase to production, PAM-STAMP enables you to virtually develop and validate almost any sheet metal forming process and the setup and analysis of automotive hemming processes.
The solution offers simple-to-use, dedicated process templates, and workflows for most sheet metal forming processes, for example, tube-bending, hydroforming, and flex forming, allowing even engineers with limited experience to produce high-quality simulation outcomes. Thanks to the program's extremely open environment it is also an excellent tool to support experts and researchers with their (innovation) challenges, by allowing them to control in-depth not only process-related parameters but FEM-related numerics as well.
PAM-STAMP enables the successful production of sheet metal parts, sub-assemblies, and assemblies, whether working with simple or complex geometries, conventional steel, or advanced lightweight materials. With its process-driven, intuitive graphic user interface and a highly accurate solver, PAM-STAMP delivers precise results for cold, warm, and hot sheet metal forming processes.
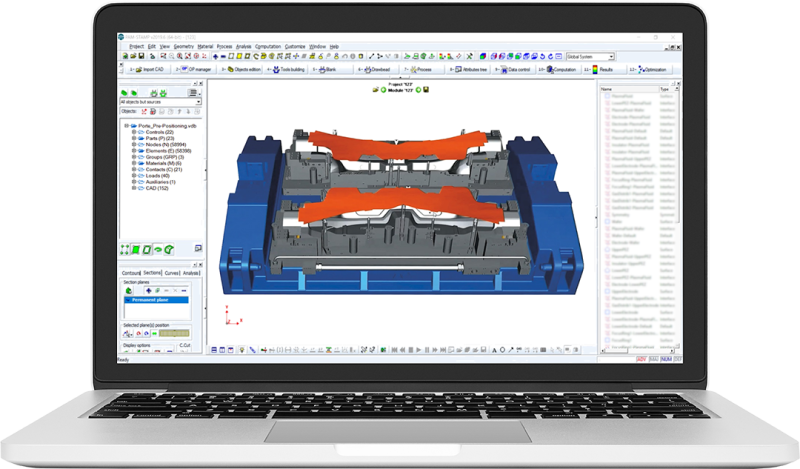

Flexible
Simulate almost any sheet metal forming process

Process Driven Set-up
Use, modify, or create process templates for effortless setup of even the most complicated processes

Accelerate Innovation
Build your processes, including detailed process and numerics control

Accurate
Accurate physics representation integrated in the solver for materials and process to achieve the highest predictive confidence

Productive
Compute even the largest models in a short timeframe with excellent solver scalability

Proven
25+ years of proven reliability across industries