ESI launches PAM-STAMP 2017 and Delivers Drastic Efficiency Improvements
Paris, France – February 9, 2017 – ESI Group, leading innovator in Virtual Prototyping software and services for manufacturing industries, announces the latest release of ESI PAM-STAMP; simulation software dedicated to sheet metal forming. An end-to-end solution, PAM-STAMP covers cold, warm and hot forming processes, and most special processes for all types of metallic materials. Used in all industries, ESI PAM-STAMP provides a full solution to manage progressive, transfer and line dies and also tool surface design. From the first feasibility iterations on the part design to the final validation of the entire stamping process, PAM-STAMP delivers fast and reliable results, addressing thinning, splitting, compression, wrinkling, trim line optimization, spring back and die compensation, using ESI’s Triple Speed technology. ESI PAM-STAMP enables die face designers and sheet metal forming engineers to manufacture parts right first time.
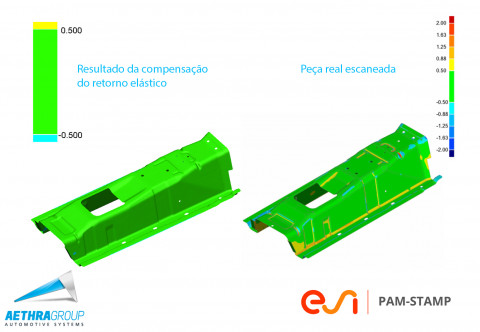
usando o PAM-STAMP, o cliente Aethra obteve uma excelente correlação entre a peça simulada (após a compensação do retorno elástico) e a peça produzida (dados de leitura digital).
With the latest version of ESI PAM-STAMP 2017, considerable efficiency improvements have been achieved when working with complete line dies. Importing the geometry, setting up, and analyzing line die simulations has become as fast, easy and straight-forward as when working with only one operation! It is a huge step forward and makes working with ESI’s sheet metal forming solution PAM-STAMP even more enjoyable and efficient
says Arlem Picinin, AETHRA, Brazil.
The release of ESI PAM-STAMP 2017 delivers major efficiency improvements for setting up progressive, transfer and line dies. ESI engineers have redesigned the User Interface (UI) in order to significantly reduce the number of “clicks” and drastically increase work efficiency. Setting up processes is now done directly following a new and streamlined horizontal workflow, facilitating the setup of the entire stamping process; end to end.
Also new in PAM-STAMP 2017, a centralized ‘Operations Manager’ enables easy definition of the global layout for multiple operations. The stamping process is managed by a completely new ‘Process Editor’. Kinematics can be quickly defined per operation, and users can easily add, modify, or remove tools.
Beyond processing geometrical draw beads imported with the die face design, it is now also possible to generate geometrical drawbeads based on the information provided with equivalent draw beads, in one click and fully automatically.
Analysis of a process is executed with the accurate PAM-STAMP Solver, by default running now in Triple Speed mode; a technique developed by ESI Group to speed up stamping simulations by a factor 3 to 5. Triple Speed has been validated over several years and avoids the disadvantages of commonly used techniques to speed up simulations. Only from ESI, it is the key to getting accurate results in the shortest possible time: something especially important in the early phase of a project.
In the new PAM-STAMP, a streamlined workflow and efficient numerical techniques were added to take into account the elasticity of tooling. Advanced simulation, incorporating detailed modelling of tools and dies, is easily achieved for final validation.
For more information about ESI PAM-STAMP, please visit www.esi-group.com/products/pam-stamp
Join ESI’s customer portal myESI to get continuously updated product information, tips & tricks, view the online training schedule, and access selected software downloads: https://myesi.esi-group.com
For more ESI news, visit: www.esi-group.com/company/news
ESI Group – Media Relations
Celine.Gallerne [at] esi-group.com (Céline Gallerne)
+33 1 41 73 58 46