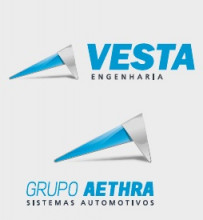
Vesta Engenharia Compensates for Highest Springback to Date with ESI PAM-STAMP
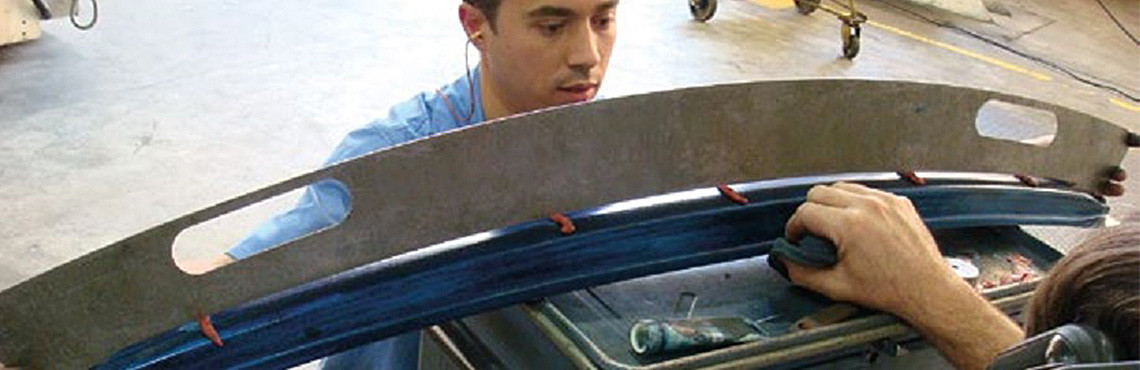
Successful springback compensation is the result of a stable and robust process, knowledge of the product demand and a good understanding of the software results.
Bernardo Perillo, Ricardo Micheletti Viana, Wellington Caetano SoaresMechanical Engineers/ VESTA Engenharia
Story
VESTA Engenharia, founded in 2011 from the AETHRA Group, is an independent company which aims to provide high quality services in a variety of engineering fields, such as automotive, aerospace, mining and metallurgy, naval, renewable energy and steel.One of the products VESTA manufactures is a vehicle bumper. (Fig.1) The bumper is made in a single action stamping operation from a dual phase steel material. This high-strength steel with both a ferrite and a martensitic microstructure causes it to have a springback behavior that is much more difficult to compensate than with conventional steel. For some reason, in this case, the springback values were significantly higher than usual.
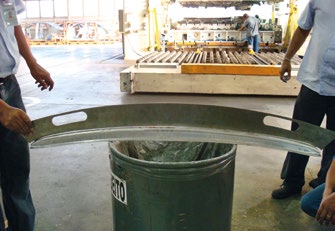
This soon became more than just a negligible problem. VESTA began studying ways to stabilize the part and improve feasibility. It involved the OEMs into open-minded, constructive product co-design activities, considering the effects of the design on the process itself to attain feasible springback compensation.
VESTA was already an experienced user of ESI PAM-STAMP, ESI’s sheet metal forming simulation solution, which it routinely used for springback compensation on other products. Knowing how well PAM-STAMP was able to counter this issue for its other tools, VESTA submitted this challenging part to the simulation tool.
Quickly, the engineers identified a +/-10mm maximum deviation compared to the nominal part (Fig.2). Such high value was a shock for all engineers, but considering the characteristics of the dual phase material and trusting in the results of PAM-STAMP, they decided to move forward with the results and compensate for the large deviation. PAM-STAMP prescribed a +/-13mm compensation on the die. This was such a drastic modification that, had the springback results been wrong, the tool would have completely gone to waste.
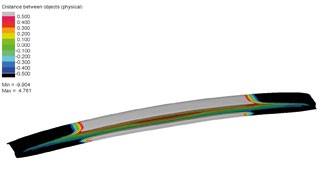
After having modified the tool, during the very first attempt, VESTA was rewarded with results that were consistent with what PAM-STAMP had calculated. The springback effect on the part was kept within the tolerance (Fig.3), allowing VESTA to avoid any further, costly, time-consuming tool modification iteration on the shop floor.
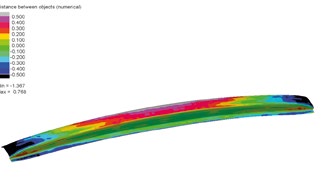
Looking at the big picture, its consistent use of PAM-STAMP allowed VESTA to build the knowledge, experience, and confidence to carry out this type of work and to be seen as a trusted leader by its customers.
About VESTA ENGENHARIA
VESTA ENGENHARIA was founded in 2011 from the company Aethra Group, one of the largest industries in the manufacturing of automotive components with high quality products. VESTA EN-GENHARIA is an independent company which aims to provide high quality services in many fields of engineering such as automotive, aerospace, mining and metallurgy, electronic and automation, naval as well as engineering for renewable energy and steel.
For more information visit Vesta Engenharia
Story release date: May 28, 2015