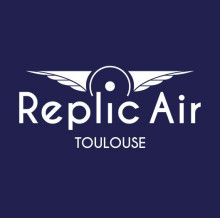
通过3D打印仿真,在航空领域实现新旧概念融合
与 ESI 团队合作,使我们解决了系统的制造问题。 借助 ESI 增材制造模拟解决方案,我们能够做出正确的决定,在尽可能短的时间内交付飞机发动机冷却系统的部件。
Wilfried DUFAUDAura-Aero联合创始人和replic 'Air创新领导者,致力于AM应用和科学课题研究
案例背景
在一场技术革命中,无论是自动驾驶汽车、机器人还是无人机,都会面临“旧的东西被淘汰,新的东西被吸纳”的境遇,新事物虽然令人期待,但也不得感谢历史曾带给我们丰富的经验。Replic航空协会在这次研究中完成了一次完美的新旧结合,实现了新事物与历史概念的重叠。Replic航空协会创建于2011年,由一群来自空中客车(Airbus)和赛峰(Safran)等不同公司的航空爱好者组成。目前,他们准备将上世纪40年代的概念飞机Dewoitine 551重新设计和制造,并计划首次试飞。
A key component to the success of this project is partner collaboration. Réplic’Air enlisted the support of Expleo (formerly Assystem Technologies) and PRISMADD to produce and deliver unique 3D printed metal parts to equip the aircraft – specifically for the engine’s cooling system, an assembly of five manifold blocks of pipes and reservoirs. Expleo is an engineering group who assists its clients in their digital transformation whereas PRISMADD is dedicated to the realization of its client’s parts – simple to complex, often through 3D printing.
Initially, the supporting partners redesigned and manufactured the 3D printed replicas for the engine’s cooling system without the benefit of simulation. This led to unanticipated distortion, porosity and gaps between layers (particularly due to thin walls) – not to mention hours of time lost and materials wasted. An estimated 20K€ in materials and a one month delay resulted from every two defective prototypes produced. To meet their deadline for a fully functioning plane, they realized that simulation would help them identify the best design for their parts in the shortest timeframe possible. For this, Expleo turned to the simulation software they apply to their own 3D printing needs, ESI Additive Manufacturing simulation software.
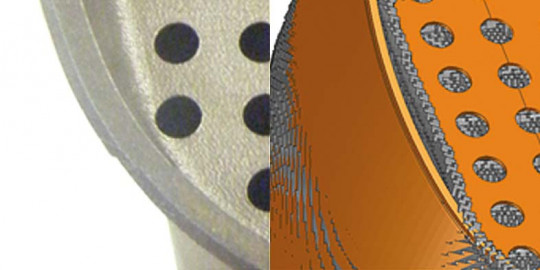
With the confidence of highly accurate simulation results, established on more than 10 years of Additive Manufacturing project collaboration experience using ESI Services, the project team quickly identified thesource of problems and modified by:
- increasing body wall thickness in specific areas to limit distortion and porosity of thin walls in the 3D printing process
- repositioning an anti-sloshing grid to avoid the edge distortion and enable a seamless, “watertight” assembly
- adjusting the surrounding support strategy to significantly reduce the distortion-induced porosity.
Through effective simulation of the Additive Manufacturing process, the team was able to evaluate multiple iterations and arrive at an improved design. ESI Additive Manufacturing simulation enabled Expleo and PRISMADD to develop and produce all five components correctly, on the first try, in the shortest timeframe, and for the least amount of money – which certainly pleased Réplic’Air.
About Réplic’Air
Created in 2011 by a core of enthusiasts of Aeronautics, the Répilc'Air association wants to revive the spirit of our pioneers and promote aerospace. Today, it has about eighty members of all ages and all backgrounds.
For more information visit Réplic’Air