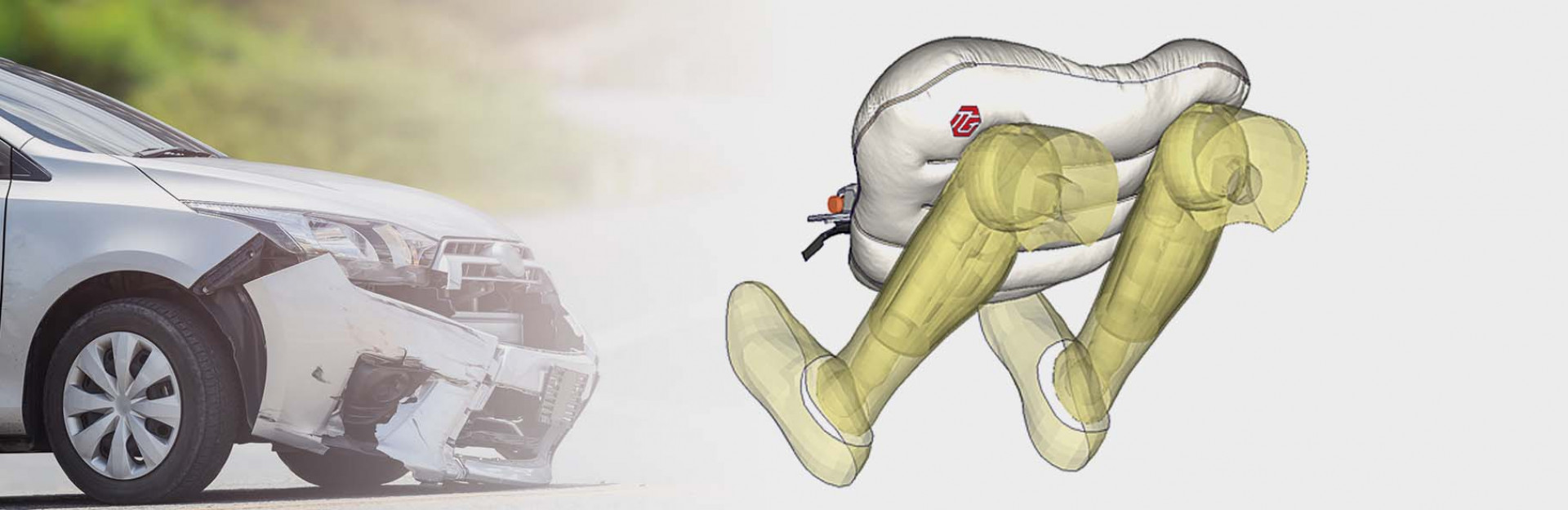
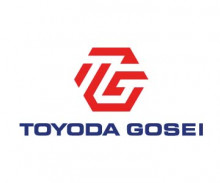
Toyoda Gosei Europe réduit ses délais de moitié à l’aide du prototypage virtuel
“ Grâce au module airbag d’ESI Virtual Performance Solution utilisé pour le pliage et la couture des airbags, la précision et les délais de développement d’airbags genoux complexes ont été grandement améliorés. Outre ses logiciels très pointus et conviviaux, ESI a déployé une assistance remarquable qui a permis à Toyoda Gosei Europe d’améliorer significativement son processus de développement à base de simulation. ”Alexander Diederich Group Leader CAE Toyoda Gosei Europe
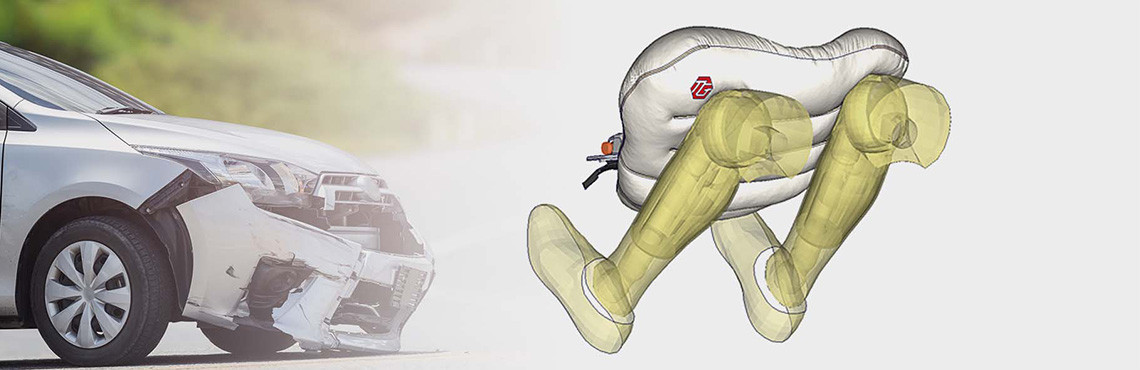
By using ESI Virtual Performance Solution’s airbag module for airbag folding and sewing, the accuracy and lead time for developing complex Knee Airbag (KnAB) have improved drastically. Besides the advanced and user-friendly software products, ESI’s outstanding support allowed Toyoda Gosei Europe to further improve our simulation-driven development process significantly.
Alexander DiederichGroup Leader, CAE Toyoda Gosei Europe
Story
Ever-changing automotive safety regulations constantly put pressure on suppliers to build better products within shorter lead times. For Toyoda Gosei Europe (TGE), faced with the challenge of shortening the lead time to build Complex Folded Knee Airbag models (KnAB), they turned to Virtual Prototyping to optimize their airbag. This virtual prototype had to account for manufacturing by virtually modeling the airbag’s folding and sewing processes.
Initially, TGE was creating their models using various simulation codes, which resulted in long lead times because they had to conduct iterations with code modifications and model exchanges. Additionally, they were not using the same tools as their colleagues overseas and therefore had to deal with time-consuming communication and multiple data exchange.
Using ESI Virtual Performance Solution (VPS), TGE built a detailed KnAB model with high accuracy and in less time, accounting for the airbag folding process. They were able to provide their customer with predictable simulation models for various types of crash simulations, even for Out-of-position (OOP) scenarios. Additionally, TGE investigated the robustness of the complete KnAB module as well as the robustness of single parts within the KnAB assembly early in the developmental state. This level of prediction of the simulation model has been the basis for several product decisions and improvements at TGE since the deployment of VPS.

Robustness study of protection cloth; physical test (left); with ESI Virtual Performance Solution (right).
Proven by CT scans, the accuracy of the models exhibits the high-quality achieved by the newly implemented modeling process and confirms the capabilities of VPS. Besides reducing their costs – by limiting the number of physical prototypes, increasing the accuracy of their models, and implementing a new assembly procedure – using the VPS airbag module allowed TGE to cut the time needed to build complex folded KnAB by half, while at the same time increasing the quality of their product. The team can now allocate more time to tasks that are important to their customers rather than struggling to exchange data between departments or countries.
Learn more about the Future of Mobility
For more information visit Toyoda Gosei
Story release date: September 17, 2019