BM-STAMP
BM-STAMP
Automotive Stamping Simulation Software
BM-Stamp: The Smart Choice for Automotive Stamping
Predicting part quality early in automotive manufacturing is crucial because relying on physical tryouts can be costly and time-consuming when unexpected defects occur and need to be corrected at this late phase in the engineering cycle.
Body Manufacturing-Stamp (BM-Stamp) from ESI is a cost-attractive simulation solution that empowers automotive part manufacturers to optimize their stamping processes, reducing the reliance on physical prototypes, and improving the precision and quality of manufactured parts from early on in their project lifecycle.
BM-Stamp provides an extremely easy-to-use graphical interface enabling precise stamping validation for all automotive materials without requiring engineers to have FEM or other numerical expertise, enabling highly predictive formability, accuracy, and aesthetic results in a consistent manner.
Recognized as a trusted engineering partner, ESI delivers precise validation for engineers to consistently achieve top simulation results, and as a consequence reduce overall costs, and accelerate production timelines.
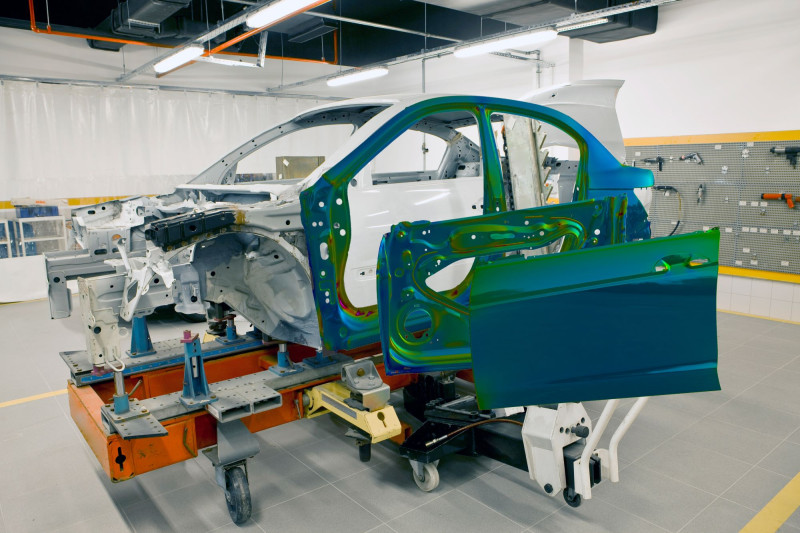
What our clients say...
"BM-Stamp has significantly enhanced our sheet metal forming simulation accuracy, particularly for challenging materials like aluminum," said Ghislaine Couturier, Stellantis. " For a large aluminum hood inner with up to 10mm of spring back, it accurately predicted 95% of the geometry within 0.5mm of the scanned part. This impressive predictivity, coupled with great usability that allowed us to easily deploy to more than 25 users, enabled us to significantly improve simulation accuracy throughout the process, including during early feasibility. As a result, the % of geometrical and cosmetic conformity of first parts, a key KPI for the stamping department, is expected to improve drastically, delivering a direct reduction in tool investment costs-late modification rate, and project lead times."
Ghislaine CouturierStamping Innovation Manager, Stellantis

Unlimited Virtual Try-Out
Explore alternative stamping process routes and the effectiveness of countermeasures

Unparalleled Predictiveness
Accurate physics modeling for excellent formability, springback and surface aesthetics prediction

Intuitive Interface
User-friendly graphical interface with stamping process-oriented workflow, full CAD-based setup

Process Coverage
Specifically designed for key automotive stamping processes

Fast Start
Minimal ramp-up time to become productive; hours instead of days

Proven & Scalable
Stamping solver technology with over 25+ years of proven track record in predictiveness, high-performance computing capabilities
Key Values Delivered by BM-Stamp
- Minimize Cost and Time in Physical Try-Out: Validate the stamping process by predicting and eliminating formability issues (e.g. cracks, wrinkles), compensating for springback and ensuring required cosmetic surface quality before any physical tool is milled.
- Reduce your current total cost-of-ownership for stamping simulation software: Reduce your current stamping software budget or increase your computational capabilities through attractively-priced flexible token licenses.
- Guarantee Manufacturability: Ensure design intent can be achieved without manufacturing or cosmetic issues through highest predictive confidence.
- Minimize Material Cost: Through accurate blank outline prediction.
- Minimize Time Between Try Out and Production: Ensure upfront the required part quality for selected press line(s).
- Obtain Highest Aesthetical Quality: Use dedicated contours for the detection of possible surface defects and conduct shopfloor-like analysis in a virtual lightroom to realistically assess location, size and severity of identified defects.
Main BM-Stamp Applications
- Validate the final part quality by applying full stamping process validation for hot and cold formed sheet metals.
- Evaluate and eliminate surface defects by using a virtual light room environment.
- Minimize material utilization and waste.
- During the stamping process, include elastic tool and press deformations for large parts and high strength steel components.
- Predict, control and compensate springback (in single or multiple operations).
- Determine accurately the minimum required press force to ensure part can be manufactured on a selected press.
Want a more detailed insight into the full capabilities of BM-Stamp?
Register for our upcoming webinars to learn more.

Harness the power of BM-Stamp Simulation for the following Key Automotive Stamping Processes:
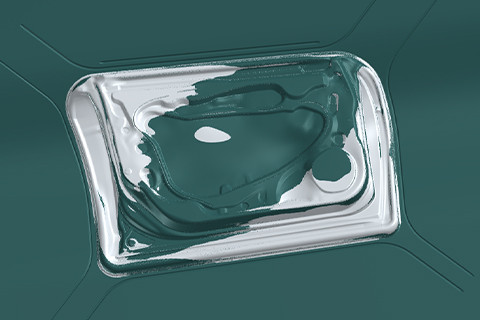
Mastering High-Strength Steels & Aluminium
BM-Stamp's cutting-edge physics solver delivers highly accurate predictions of manufacturability and springback magnitude, addressing the demands of stronger, thinner high-strength steels and aluminum.
The result? The innovative multi-operation spring-back compensation feature ensures every part meets stringent dimensional tolerances. Additionally, the accurate calculation of contact forces allows for easy evaluation of the minimal required press force, facilitating the selection of a press line with sufficient power to produce parts correctly.
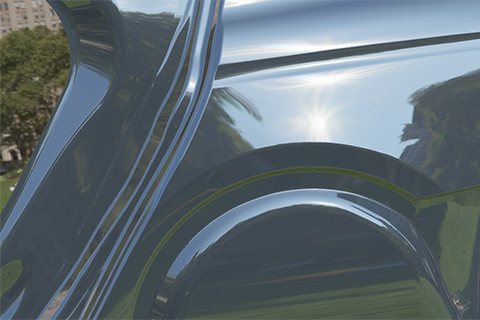
Elevating Surface Quality with Precision
An extensive set of dedicated post-processing options is available to explore the location, size and severity of cosmetic defects, from standard contours to digital stoning and a virtual lightroom, including a high-quality rendering engine.
The result? Even at early stages of your project, accurately predict cosmetic defects allowing informed decisions and analysis of the effectiveness of proposed countermeasures, drastically reducing the risk of finding defects during physical try-out.
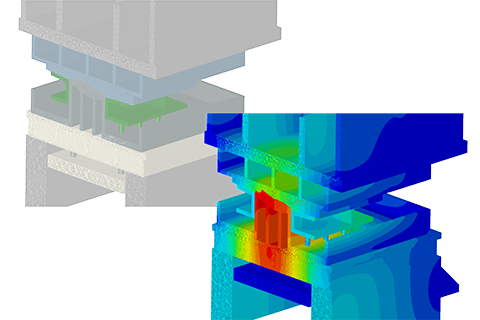
The Virtual Try-Out Space
BM-Stamp integrates full 3D die geometries and comprehensive press descriptions into standard stamping simulations with minimal additional calculation time, capturing small elastic deformations of tools and presses throughout the stamping process.
The result? This integration provides the most accurate local contact conditions, influencing the blank’s material flow and altering local stress fields. By running a trial at the end of the stamping validation process, you can verify that parts meet specifications, ensuring consistent delivery of the highest quality products.
Download the brochure to learn more about how to achieve superior quality stampings in Body & Chassis Manufacturing, ensuring defect-free sheet metal formed components...
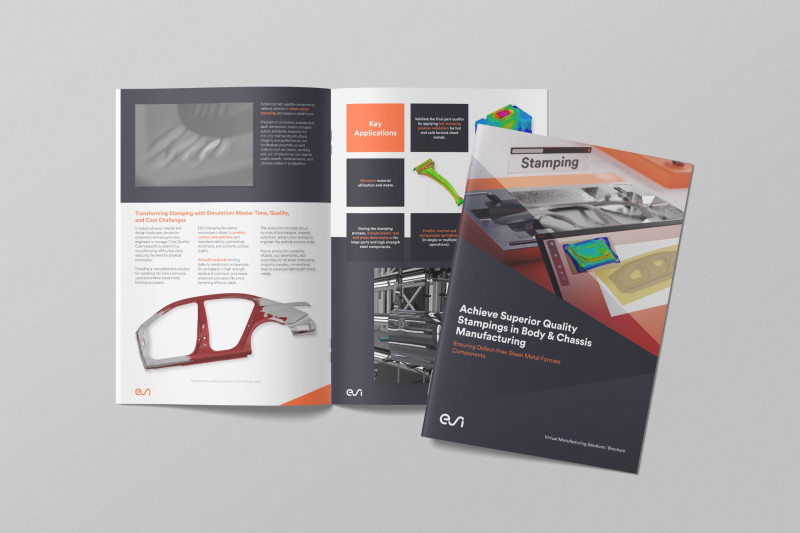