High passenger expectations, global competition, and growing program complexity are making it more challenging to accelerate innovation while driving production efficiency. Aerospace OEMs and suppliers alike must ensure the highest levels of quality, performance and safety, while meeting strict regulations, production agility, and program costs.
Virtual Prototyping provides better ways to validate the performance of your design, assess the manufacturability, and define the most efficient manufacturing process; allowing you to meet your objectives in terms of cost, time, quality, program sustainability, and customer satisfaction.
Are you an industry leader in the development and manufacturing of modern aircraft technology and want to see your company pioneering the evolving aerospace industry? Connect with ESI’s virtual prototyping expert and learn about how global players in the industry have been applying ESI Virtual Prototyping and Manufacturing Solutions to:
- Revolutionize the assembly process with Human-Centric Assembly Validation
- Increase Passenger Comfort with Interior Engineering & Acoustic Design
- Optimize Cost, Time and Quality for high precision Part and Component Manufacturing
Cabin and Cockpit of the Future: Make the Right Decisions Early
To enhance the overall passenger experience, it is critical to ensure that your aircraft interior and seat design meet the proper quality and comfort requirements without hindering the on-time certification, safety and production targets.
Virtual Prototyping enables you to immerse yourself in new ideas, test innovative solutions and deliver the next steps in the evolution of the passenger experience. It allows designers and engineers to quickly explore your most inspiring designs for ultimate passenger comfort, performance, seat design and layout as well as meeting strict regulations and production costs.
Experience your Products & Processes as Good as Real
As design sets the stage for manufacturing and service, engineering teams must recognize the interactions of people with their proposed products and processes to ensure ease of production and maintenance.
The use of Virtual Reality during the design review process to conduct human-centric assembly and maintenance validations significantly reduces risks to operator safety, improves on time delivery, delivers repeatable quality, and ultimately improves product profitability.
Discover how Safran Nacelles visualizes and validates its process design, without relying on physical prototypes.
Ensure High Precision, High Quality Parts at the Lowest Cost
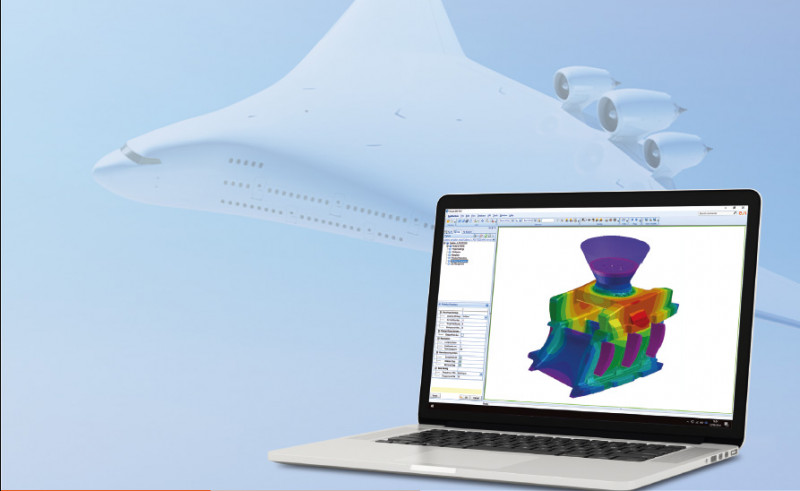
The highly competitive aerospace market and its growing industry demand are driving significant program cost reductions, hence pressuring aerospace part manufacturers and suppliers to develop extremely efficient manufacturing processes. Virtual Prototyping is one of the innovative ways they’re able to minimize cost overruns, prove manufacturability and process consistency, and ultimately produce high quality, cost-efficient parts & complex components on time.
For airframes and aero engine components, Virtual Manufacturing accelerates the development and validation of key manufacturing and joining processes to fabricate complex and light-weight components with the specified quality. Applied in standard development and production processes, smart manufacturers virtually streamline manufacturing capabilities, secure novel production techniques such as, and develop and validate composite designs.