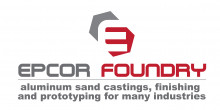
Speeding Past the Competition: Epcor produces quality parts faster than their competitor with ESI QuikCAST casting simulation solution
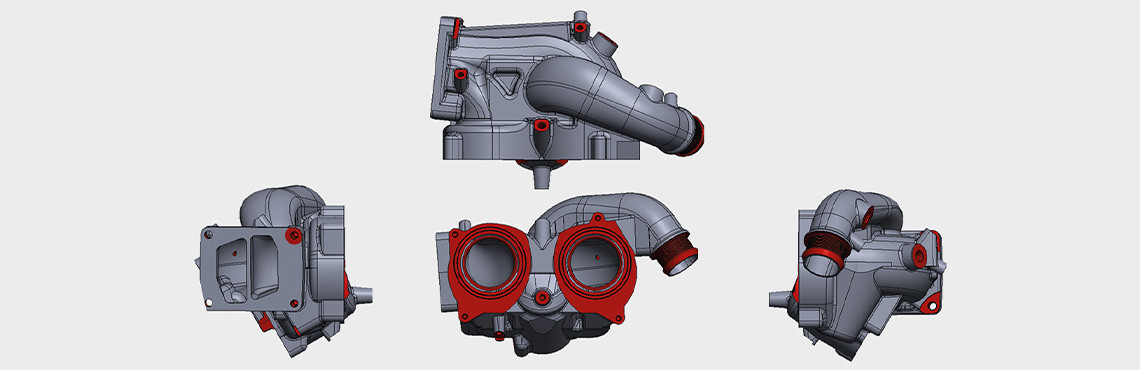
We tried QuikCAST on a few trial parts and found that it was able to accurately simulate our molding results. It provides a more effective approach than what we were doing before because it makes it possible to look into / at the casting process one step at a time.
Mike MarattaPlant Manager / Epcor Foundries
Story
Cincinnati-based Epcor Foundries was able to win business away from its competitor who failed to produce quality exhaust gas recirculation (EGR) valves for their automotive parts manufacturer in the required time.
Although they were happy to gain the business, Epcor knew it would be a challenge to get this intricate part into production quickly while avoiding typical casting manufacturing problems, like shrinkage and porosity.
The standard approach for foundries is for patternmakers to design molds based on their own experience. This method is less than optimal for various reasons, the number one reason being that the initial design is rarely viable.
In the case of the EGR valve, Epcor knew they could not meet the customer’s aggressive delivery requirements using the traditional approach. Therefore, after evaluating different casting simulation tools, Epcor turned to ESI QuikCAST. In addition to it being an affordable and easy-to-use solution, Epcor liked the fact that QuikCAST linked them to ESI’s more powerful and comprehensive casting simulation program, ESI ProCAST.
To begin, Paul Kiefer, Senior Design Engineer for Hitech Shapes and Designs (an affiliate of Epcor Foundries) performed the simulation of the EGR valve’s casting process. Starting from a CAD model of the valve, Kiefer defined the casting process parameters along with material properties and used QuikCAST to produce a simulation that allowed the team to visualize mold filling and solidification – and eventually predict the part’s quality. From this, they determined that adjustments were necessary due to shrinkage porosity in certain locations of the part (Fig. 1).
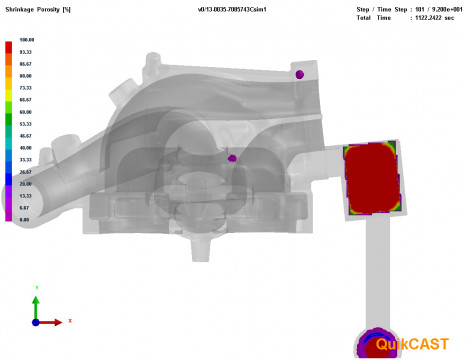
At this point, it was important to analyze the results further in order to understand the evolution of this porosity during solidification.
Kiefer determined that, in several critical areas, the molten aluminum was solidifying early in the cooling process and creating isolated pockets of liquid metal that could not be fed through because the path to the feeders were cut. This is what caused the shrinkage porosity. A defect like this could actually cause the part to fail during its usage. If they found this defect on the shop floor, instead of in the design phase, it would have meant a delayed delivery, leading to a shutdown of the auto manufacturer’s line due to lack of parts.
Once the baseline simulation model was ready, Epcor could begin making the necessary modifications to eliminate porosity. Kiefer considered several approaches to address the problem but settled on adding risers. In doing so, shrinkage would occur in the risers and not the casting.
A final run of the part with QuikCAST revealed that the problems were resolved and that the mold would produce quality cast parts on the very first try and each time after that (Fig. 2).

Ultimately, Epcor was able to build the mold design verified by QuikCAST. The mold produced good parts from the first run, exceeding their customer’s expectations.
“Our customer was very pleased that we were able to get the new casting up and running so quickly,” says Maratta. “This helped avoid the downtime that our customer would have experienced if there had been significant delays during the process. The startup time and throughput levels were where they needed to be at the start of a program for a complex casting with tight quality requirements.” He goes on to emphasize, “The customer was very happy with our ability to launch such a complex part without any issues.”
About Epcor Foundries
Epcor Foundry is a division of Seilkop Industries, Inc. Seilkop Industries consists of four individual companies specializing in aluminum sand casting, die making, CNC pattern making, Blanchard grinding, burnout, roll grinding and equipment repair. Since 1946, Seilkop Industries, Inc. has the in-house capabilities of taking your projects from design to prototype to production to finish. Our focus is on solving your manufacturing needs with highly specialized application-based solutions.
Epcor is a privately owned, ISO certified, green sand aluminum casting foundry that specializes in prototypes and medium to high volume castings for several industries, including automotive. We are known for precision craftsmanship, especially for complex and highly cored leak tight castings.
For more information visit Epcor Foundries
story release date: August 16, 2016