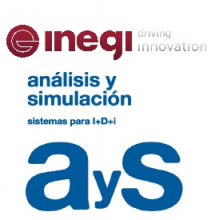
Inegi Uses ProCAST to Manufacture Customized Hip Prostheses in a Cost Effective Way
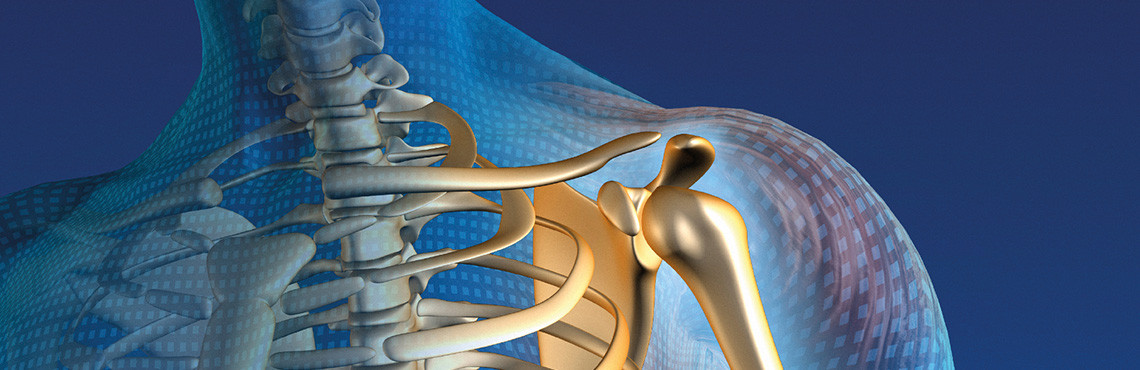
“Scientific methods can always save us time and cost. ProCAST is just that tool helping foundry men find the right solutions. For the investment casting process, ProCAST can generate different layers of shells and with wrapping outside. This helps predict the temperature field more precisely.”
Nannan SongSenior Researcher Advanced Foundry and Rapid Prototyping Technologies / Inegi
A hip prosthesis (Fig.1) is a highly customized product, tailored to the exact morphology of a patient. Yet whatever the complexity in its design, it is expected to withstand an equivalent of over one million cyclic loads each year during its functional life inside a human body.
Although modern medical imagery allows a very accurate design based on the patient’s characteristics, manufacturing with such high specification levels is still very widely based on a trial and error methodology, which is both expensive and time-consuming.
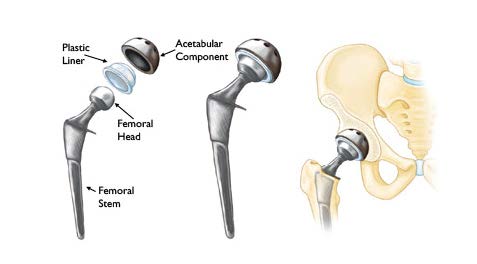
Inegi, a non-profit organization in Portugal providing R&D support to a broad range of industries, has elected to turn to simulation to identify the most efficient process design suitable for a specific prosthesis. Their challenge has been to reduce casting defects, such as shrinkage porosity and residual stress, as these can accelerate fatigue failure and reduce the life of the prosthesis. The aim is to improve the patient’s comfort and safety while reducing costs of manufacturing and replacing prosthesis.
Product and Process Design
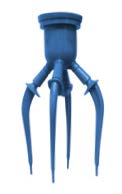
Investment casting is best adapted for products with unique features requiring exceptional precision. To manufacture a hip prosthesis, a prototyping machine must produce the prosthesis model along with its carefully designed gating system. The prototyped model is then used to shape a wax pattern (Fig. 2), which in turn is the basis for the investment casting process.
A typical stem of a hip prosthesis can be anywhere from a few mm in thickness up to 2 cm, while the length could be between 10 and 15 cm. Such high length-to-diameter ratios typically create low-temperature gradients during the casting solidification. This leads to centerline shrinkage along the stem section, which can reduce the product lifetime. Also, feeding of the stem is from the prosthesis head, through a neck narrower than the connected stem, which reduces the feed length. The neck & head themselves are susceptible to shrinkage porosity.
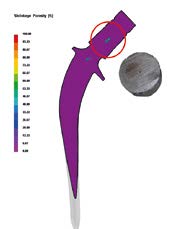
Figure 3 shows shrinkage porosity validation on a cut section sample in the prosthesis head. In these conditions, the solution to avoid defects would then have to involve a mix of modified gating and process re-design. A trial and error method to eliminate undesirable porosity in the prosthesis would prove both time-consuming and costly, as several models would need to be produced, starting from the prototype stage, to achieve a suitable wax pattern.
The Switch to Simulation
Initially, the design and production of such hip prostheses at Inegi was achieved by conducting trial outcomes directly on the shop floor. Typically various trials were made with different casting and shell preheating temperatures, all unsuccessful. The resulting products were often unsatisfactory, exhibiting centerline shrinkage and having an undesirable surface finish.
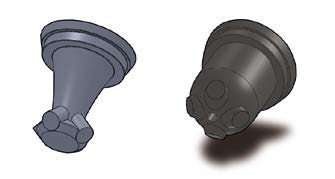
Because of these difficulties, Inegi sought the assistance of Análisis y Simulación and ESI’s ProCAST simulation software. To obtain the high-temperature properties of the specific Ti6Al4V alloy used for the prostheses they used ProCAST’s thermodynamic database. ProCAST also helped Inegi obtain greater insight into the best filling sequence and the consequent temperature gradients at various sections in the casting and shell.
Inegi was able to set up different groups of simulations, used to determine the best-adapted gating design (Fig. 4). Inegi created a unique wrapping configuration around the shell, managing the heat distribution to maintain the feed path to the stem region during the solidification process. Castings produced with this configuration were free from any centerline shrinkage and can be expected to meet the high-performance requirements of the hip prostheses. Their surface finish was improved by changing the face coat material of the shell. The high level of quality of the produced hip prostheses was confirmed by x-rays (Fig. 5)
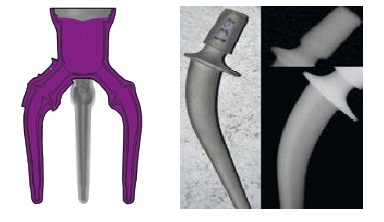
Based on this success, Inegi continues using ProCAST to simulate their casting processes.
About Inegi
INEGI is an interface Institution between University and Industry, oriented to the activities of Research and Development, Innovation, and Technology Transfer. It was founded in 1986, by the Department of Mechanical Engineering and Industrial Management (DEMEGI) of the Faculty of Engineering of the University of Porto. Being a non-profit private association and recognized as being of public utility, INEGI is currently considered an active agent playing a significant role in the development of the Portuguese industry, and in the transformation of its competitive model.
For more information, visit Inegi
Story release date: March 12, 2014