IC.IDO
Virtual Reality Engineering Software
Transforming Engineering and Manufacturing in Virtual Reality with IC.IDO
Innovative VR Solutions for Modern Product and Process Validation with a Human-Centric Approach
IC.IDO empowers engineering managers and planners with advanced VR technology, offering true-to-life virtual prototypes and real-time simulations of assembly, operation, and maintenance processes, by enabling unlimited virtual tryouts, IC.IDO reduces reliance on physical prototypes, accelerates product development cycles, and shortens time to market. Enhance collaboration, mitigate risks, and ensure efficient, successful production with IC.IDO’s cutting-edge virtual reality solutions.
Why Choose IC.IDO for Your Product & Process Validation Needs?

Enhanced Decision-Making
Gain deeper insights and make informed trade-off decisions through realistic virtual simulations.

Seamless Collaboration
Enable effective teamwork with cross-functional teams through shared VR experiences.

Shorter Product Lifecycle
Adapt quickly to market demands with faster development cycles enabled by realistic virtual tryouts.

Risk and Inefficiency Reduction
Identify and address design, manufacturing, and serviceability challenges early.

Digital Trust
Build confidence in products and processes at every milestone stage of development.

Robust Physics Engine
Provides real-time simulation capabilities for comprehensive analysis.
3 Ways to Utilize VR Technology in Your Manufacturing and Engineering Processes
Product and Process Validation: Packaging and Space Claim
Virtual reality with IC.IDO allows customers, assembly workers, and technicians to experience new products digitally before final decisions are made. Teams can review proposed products and processes well before production, providing a realistic experience of digital designs with minimal preparation. This approach leads to more successful products by allowing pre-production evaluations without the need for costly, time-consuming physical prototypes.
Enhancing Human Factors Evaluation with IC.IDO and Varjo-XR3 for Streamlined Product Development
IC.IDO, combined with OpenXR depth sensing and Varjo-XR3, enhances early evaluations of human factors like reachability and accessibility. While it doesn't replace the need for quantified measurements, it quickly identifies potential challenges, building confidence in engineering decisions through immersive, personal experiences. This technology accelerates product and process delivery by reducing surprises and minimizing late-stage design adjustments, ensuring a smoother transition from virtual review to production.
Optimizing Cross-Functional Design Reviews with Real-Time Virtual Collaboration
Experience seamless collaboration as multiple cross-functional team members come together in a virtual design review, leveraging IC.IDO's real-time simulations to validate and optimize complex designs. Watch as engineering, manufacturing, and service teams interact in a shared virtual environment, ensuring the design meets all functional and operational requirements before moving to production.
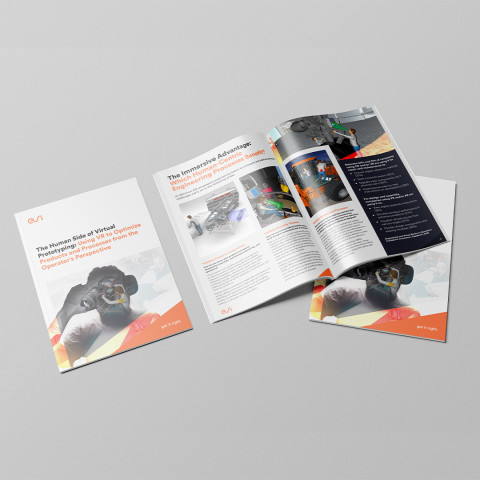
Take an in-depth look at how immersive VR technology can revolutionize how you design, manufacture, and maintain your products.
Read our ebook to learn more about how VR software enables enterprises to immersively visualize and assess products, and foster real-time collaboration to optimize decision-making throughout key milestones.
IC.IDO at a glance…
…which suits your needs the most?
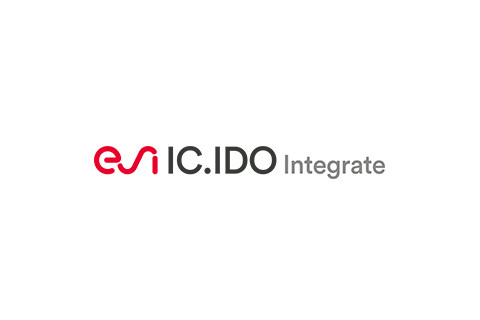
Experience Products in an Immersive Environment
-
Product packaging clearances, and integration of virtual experiences
-
Realtime interactive cable & hose simulations
-
Component installation & removal with real-time physics
-
Experience tooling and mechanism interactions
-
Visibility, reachability, & accessibility firsthand experiences
-
Collaborate directly with other IC.IDO Integrate or IC.IDO Build & Maintain interfaces
-
Share engineering outputs upstream and downstream in your value chain
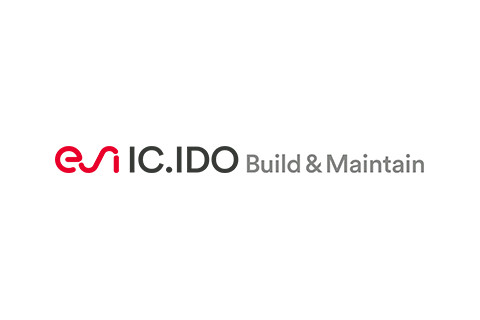
Conduct Human-Centric Process Validation Workflows & Immersive Product Integration
Includes all IC.IDO Integrate capabilities plus the following additional features:
-
Evaluate and optimize assembly processes
-
Quantify ergonomics results with manikin
-
Record Human-Process-Product interactions and share outputs
-
Collaborate directly with other IC.IDO Integrate or IC.IDO Build & Maintain interfaces
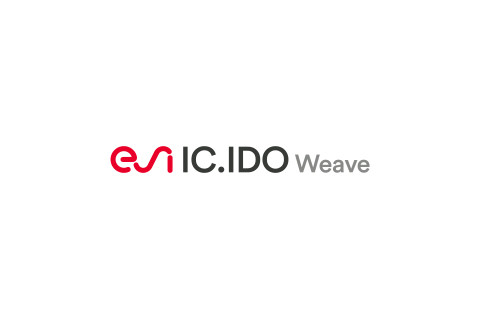
Flexibily engage with larger numbers of participants across Integration & Process Validation workflows
-
Flexible tokenized access to IC.IDO Integrate interfaces
-
Flexible tokenized access to IC.IDO Build & Maintain interfaces
-
Dedicated Multi-user (participant) collaborative virtual workspaces (CoLab)