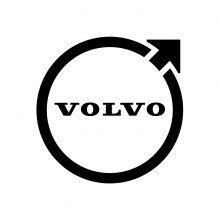
Xcelerate with Mega Casting — Shaping the Future of Body-in-White Design at Volvo Cars
Volvo Cars' strategic move to mega casting
The evolution of casting machine size has been a significant factor driving the emergence of mega casting in the die-casting industry, and Volvo Cars have made a strategic decision to transition to mega casting to transform the future of their body-in-white designs.
Traditional body structure designs involved over 200 individual parts, resulting in significant manufacturing, transportation, storage, and assembly challenges. These parts required costly tooling, individual process design, and contributed to environmental footprints. Additionally, assembly often led to out-of-tolerance distortions, necessitating rework late in the process.
Mega casting offered a transformative solution by consolidating multiple parts and processes into a single casting component, thereby eliminating many of the aforementioned complexities. For instance, Volvo successfully replaced the rear body frame, composed of approximately 100 parts, with a single mega casting. An unforgettable fact is also the influence of the total weight of the car, which becomes even more significant when discussing electromobility.
The size of the castings, as well as the fact that castings would now be part of car body assembly, suggested that they should be manufactured in-house at Volvo and stay close to the assembly plant to avoid complex transport/logistics.
To accommodate this, Volvo Cars established a large casting foundry in Torslanda, Sweden, equipped with two 8400-ton die casting machines.
Volvo Cars is also simultaneously working on setting up 2 more plants in China & Slovakia with two large Giga presses each to address the local/regional needs.
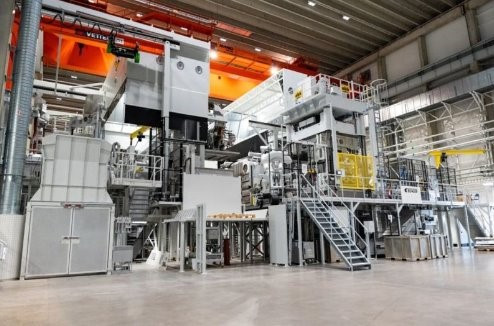
Volvo’s 8.400 T Giga Press installed at its plant in Sweden
Addressing the challenges of mega casting with simulation
The transition to designing mega casting components posed unique challenges for Volvo Cars, especially considering the stark contrast with traditional stamping methods.
Recognizing the complexity of mega casting design, “we understood that efficient part design would be impossible without the use of a highly predictive simulation tool” observed Jonas Sörensson, Manager ME Commodity - Casting at Volvo Cars, “This tool needed to handle huge models and cover all aspects of the casting process, from initial die heating and filling to solidification, ejection, and final distortion, while maintaining a close link to performance environments”. Thus, Volvo prioritized the adoption of advanced simulation technology to address these multifaceted design challenges effectively.
When deciding on the most appropriate casting simulation tool for the mega casting project, Volvo Cars initially evaluated their existing in-house casting simulation solution.
However, recognizing the significant challenges and potential risks involved, including the considerable costs associated with tool and gating design (with tools costing over €1 million per piece) and the need for accurate locking force prediction to ensure manufacturability, Volvo Cars opted to conduct a benchmark with the three leading global casting simulation providers.
This benchmarking process aimed to assess the capabilities and suitability of each simulation tool to meet Volvo Cars' specific requirements and challenges within a defined timeline. The benchmark itself consisted of a casting analysis with a focus on a pure flow simulation (temperature, pressure and piston movement), and the analysis of a mega casting component that focused on the large part handling, flow, thermal and stress results to include analysis of the final distortions after the casting process as well. At the end of the benchmark the conclusion was, based on key decision criteria like ease of model handling, calculation speed and ability to handle the various process phases (die heating, filling & solidification, ejection, quenching, trimming and distortion) that ESI and ProCAST offered the best partner and solution to assist in the casting design process and support Volvo Cars in their journey towards a mega casting future.
What is the current status of the mega casting project at Volvo Cars?

A mega casted component
After initial training in the software and supported by ESI’s casting experts, Volvo Cars performed their first autonomous simulation around June 2022.
Currently, Volvo Cars have been using ESI ProCAST simulations as their standard tool to evaluate die design and all related process aspects in the HPDC process.
“The try-out phase has successfully been completed with good agreement between simulation and physical reality after testing to correlate results with simulations. The next step is the production of the actual component” observes Jonas
Leveraging the value of mega casting for the future
Incorporating ESI's ProCAST simulation tool has proven “invaluable for Volvo Cars in optimizing die and gating designs virtually, while also validating necessary locking force parameters, before building the expensive tools for the mega casting component” states Jonas. Thanks to the learnings from this initial project, the gains for next projects can be very significant as the number of physical tests for correlation can be drastically reduced, with cost saving potential running into millions.
Moving forward, Volvo Cars plans to integrate the findings from casting simulations into their crash and fatigue performance simulations, aiming to further enhance the overall structure of mega casting components.
This strategic approach aligns with Volvo Cars' commitment to delivering the safest vehicles in the market, showcasing their ongoing dedication to excellence and innovation in automotive engineering.
Volvo Cars was founded in 1927. Today, it is one of the most well-known and respected car brands in the world with sales to customers in more than 100 countries. Volvo Cars is listed on the Nasdaq Stockholm exchange, where it is traded under the ticker “VOLCAR B”.
“For life. To give people the freedom to move in a personal, sustainable and safe way.” This purpose is reflected in Volvo Cars' ambition to become a fully electric car maker by 2030 and in its commitment to an ongoing reduction of its carbon footprint, with the ambition to achieve net-zero greenhouse gas emissions by 2040.
As of December 2023, Volvo Cars employed approximately 43,400 full-time employees. Volvo Cars' head office, product development, marketing and administration functions are mainly located in Gothenburg, Sweden. Volvo Cars' production plants are located in Gothenburg, Ghent (Belgium), South Carolina (US), Chengdu, Daqing and Taizhou (China). The company also has R&D and design centres in Gothenburg and Shanghai (China).