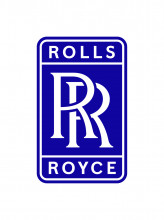
Co-design at Rolls-Royce: a “smart customer” approach to work with the supply chain for cast parts
Casting
Aerospace & Defense
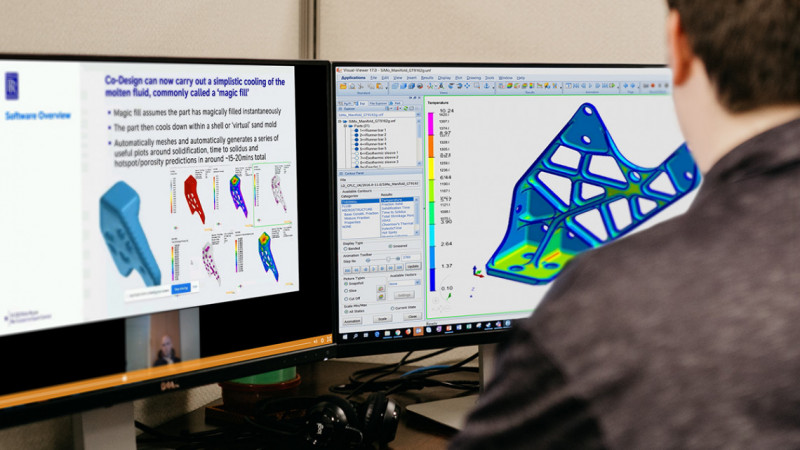
In line with its Digital First approach, Rolls-Royce engineers are shifting away from physical try-out towards a digital workflow based on ESI’s casting simulation software ProCAST. Nick Calcutt, Materials and Process Modelling Engineer at Rolls-Rolls in Derby, UK, calls it the “smart customer” approach.
With a simulation run of around ten minutes, our newly implemented co-design workflow gives us the ability to locate 97% of potential casting issues associated with designs. It is accessible to most engineers, not only FEA simulation specialists. It would be difficult to justify why you wouldn’t run a co-design simulation, especially for large and/or expensive cast parts.
Nick CalcuttMaterials and Process Modelling Engineer, Rolls-Royce