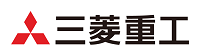
PAM-STAMP 導入事例 三菱重工業株式会社
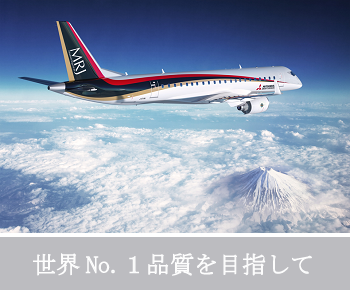
三菱重工業株式会社様の事例をご紹介します。
プレス成形解析ソリューション
使用ソフト:PAM-STAMP
三菱重工の世界トップクラス品質と高い生産性を支えるPAM-STAMP。
使用開始から半年で50%のコストダウンを実現。
三菱重工業(株) 民間機事業部 部品工作部生産技術課の藤井和慶氏、土下晋平氏に、PAM-STAMPを導入した経緯と効果について詳しく伺いました。
三菱重工業(株) 民間機事業部 部品工作部について
三菱重工業(株) 部品工作部は、同社内で民間航空機の完成機、ボーイング社などの受注部品の開発・製造を手がける部門です。部内の社員は約1900人、生産技術課は約220名です(※ 本事例に記述している数字や事実はこの事例の取材時点で公表されているものに基づきます。また数字は原則として概数で記載します)。
三菱重工業(株)の航空産業への取組み
三菱重工は、これまで民間の完成機体製造メーカーの1次下請け企業として、ボーイング767、777の胴体、最新鋭機である787の複合材主翼の製造などに携わってきました。これらの経験を活かして、今後20年間で全世界5,000機以上の新規需要が見込まれているリージョナルジェット市場に参入することを決め、2014年10月に、初のジェット旅客機であるMRJ(三菱リージョナルジェット)がロールアウトされました。
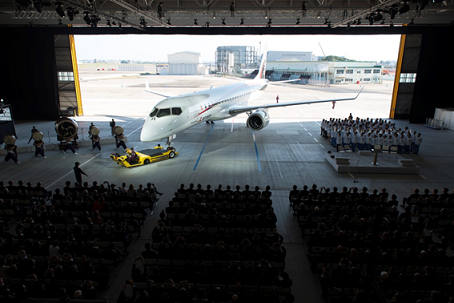
航空機の構造部品を開発・製造
― 皆様の業務内容について教えてください。
私たちが所属する三菱重工 民間機事業部 部品工作部の業務は胴体の外装板スキン)の他、ストリンガー、フレームといった構造部品の開発製造等、多岐に亘りますが、本日は話を簡単にするために「PAM-STAMPと関係の深い業務」となる「航空機の胴体や尾翼などに使うスキンの開発製造」を中心にお話することにします。
スキンは、ボーイング、エアバスなど完成機メーカー(あるいは自社内のMRJ部門)が顧客となります。つまり「受注生産による部品製造」となります。
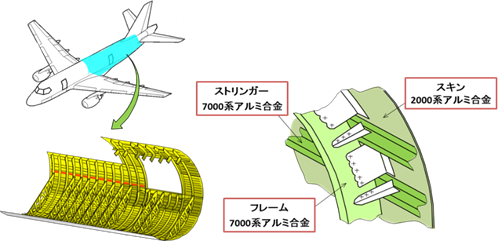
※ 以下、「三菱重工」と表記した場合、それは「三菱重工業(株) 民間機事業部 部品工作部 生産技術課で航空機の構造体を開発製造している部署」を指すものといたします。
近年の課題 – ロボット自動組み立てを前提とした高精度化
― 三菱重工 民間機事業部の最近の取り組みについて教えてください。
多くの人々を乗せて空を飛ぶ巨大な航空機、その部品製作では、最高の精度と耐久性が求められます。常に最高品質の部品を納入することは、航空機部品の事業者として「当然の前提」となります。そして近年は「最高品質を前提とした上での革新的なコストダウン」が重要性を増しています。
現在の中心課題は、「組み立て工程の自動化を前提とした部品高精度化の実現」です。従来は航空機の組み立てといえば「現場作業員が機械や工具を使って手作業で行う」という方法が主流でしたが、近年は納入先の組み立て工場(および三菱重工の工場)で「自動組み立て装置」の導入が検討されています。この場合各部品は、今まで以上に高精度で作る必要があります。人が組み立てるのであれば若干の寸法誤差は職人技で吸収・調整可能ですが、自動化された設備にはそうした調整はできないので、最初から設計者がCADで設計した通りの寸法の部品を渡さなければならないからです。
その他、製法そのものの見直しも進めています。例として「航空機の胴体外装板の裏面を、軽量化を目指して薄くする工程」において製法を変更しました。従来は、外装板の裏側を薬品によって溶かし落とす「エッチング」で対応していました。しかしこの方法は廃液処理などを含めると非常に高コストであり、かつ環境保護の観点でも望ましくありません。
そこで現在は、機械により削り込む「切削」で処理する工法に切り替えを進めています。しかし切削処理の場合、削られる方の外装板がCADどおりの板厚で成形されている必要があります。機械は指定どおり正確に削るので、結果的に外装板の一部で「薄すぎる」「必要強度が保てなくなる」など不具合が起こることがありうるからです。
今後、部品製作のあらゆる工程では自動化が推し進められていくでしょう。これは、「あらゆる工程で機械化に適うだけの高精度が厳格に求められる」ことを意味しています。
8メートル級の巨大な外装板を製作
― 飛行機の外装板というのはどのぐらい大きいのですか。
弊社が製造しているものとしては「8メートル×2.5メートル」が最大です。厚さは2.5mm~7mmと非常に薄くなっています。
材料は高強度のアルミ合金(ジュラルミン)で、製法は「ストレッチフォーミング(引張成形)」です。8メートル級の巨大外装板は1500トンの大型機械を使って成形します。この1500トン級の機械は、現在日本に2台しかありません。
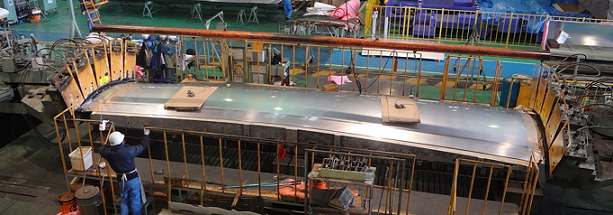
航空機スキンに採用されるストレッチフォーミングとは
― ストレッチフォーミングとはどんな製法ですか。
単純化して説明すると「巨大なアルミニウム合金(ジュラルミン)板を、その両端を工作機械の大型のジョー(持ち手)でつかんで、それを大型金型の上に載せ、1500トンの力で90秒~150秒間アルミニウム板を金型に押しつけることにより塑性変形させる」という製法です。「押しつける」と言いましたが、それは持ち手を下に引き下げてアルミニウム板を下に「引っ張る」ことにより実現させます。
一般的なプレス成形では2つの金型を使って上下の2方向から圧縮(プレス)しますが、ストレッチフォーミングでは金型は下側のみという点が大きな違いです。
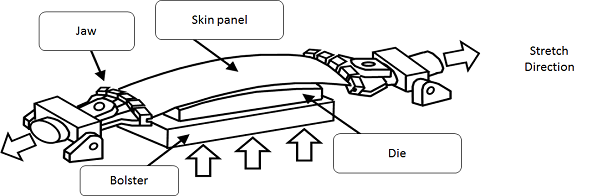
航空機のスキン成形の困難
― スキンのストレッチフォーミング特有の困難は何でしょうか。
大きくは次の2点といえます。
-
「巨大な部品を作るのに、小さい部品と同じ寸法精度が求められる」
-
「材料、金型、加工費のどれも数百万から数千万と非常に高価。やり直しは困難。『一発必中』が基本」
具体的には、以下のような課題があります。
-
「航空機のスキンでも、寸法の許容誤差は自動車と同じ」
-
「形状が意外に複雑(Rが2方向に変化する)」
-
「アルミニウム合金はスプリングバックが生じやすい」
-
「金型は数千万、材料は数百万」
自動車並の精密成形が求められる
― 困難1.「航空機の外装板でも、寸法の許容誤差は自動車と同じ」とは具体的には。
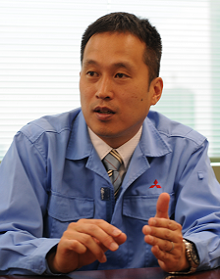
藤井 和慶氏
航空機は大型タンカーと並ぶ「地上最大級の乗り物」です。しかし、そこまで巨大であるにも関わらず、その外装板の成形において「プラス・マイナスでコンマ数ミリ」の寸法誤差しか許されません。
私は以前、自動車業界に勤めていましたが、「誤差コンマ数ミリ以内」というのは自動車の外装(ボディ)に求められるのとほぼ同じ数字です。
航空機は容積が自動車の何十倍~何百倍も大きな乗り物です。通常はサイズが大きくなれば、許容寸法誤差もそれに応じて大きくなるものです。しかし航空機ではそうなりません。「地上最大の乗り物にもかかわらず、精度は自動車と同等にしなければならない」ということです。
2つのRを持つ複雑な形状
― 困難2.「形状が意外に複雑」とは。
航空機の胴体でも主翼付近は「ほぼ円筒形(土管形状)」なので、それを構成する外装板も大きくは「正円の輪切り」になります。こうした幾何学的に均一な形状はアルミ板を円筒金型に巻き付けて成形すればよくそれほど複雑ではありません。
しかし同じ胴体でも後部から尾翼にかけての部分は、後ろに向けて次第にすぼまっていく形状です。ここを構成する外装板は縦方向(上下方向)と横方向(主翼から尾翼にかけて)の2方向に曲率(R)を持っていることになります。この複雑な形状を実現するにはストレッチフォーミングを使うほかありません。なお形状が複雑であっても、許容寸法誤差がコンマ数ミリであるのは、先に述べたとおりです。
スプリングバックが起きやすい素材
― 困難3.「アルミニウムはスプリングバックが起きやすい」とは。
いくら1500トンの力で押しつけるといっても、金属には弾性があるので少し押しつけただけでは、跳ね戻ってしまいます。即ち、スプリングバックが発生します。
アルミニウムは、特にスプリングバックが起きやすく、鉄に比べて3倍跳ね戻りやすい素材です。こうした素材でコンマ数ミリの精密成形を行うのはたいへん難しいことです。
金型、材料、共に高価
― 困難4.「金型は数千万。材料は数百万」とは
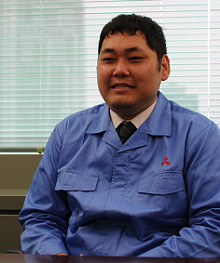
土下 晋平氏
8メートル級のアルミニウム板を成形する場合、9メートル近くの巨大金型を使いますが、この金型の製作費用は数千万に及び、また材料となる大きなアルミニウム板は、一枚あたり数百万円です。さらに、成形機では1500トンの力を数十秒継続するので、電気代などエネルギー費用も膨大になります。
金型も材料も機械稼働費も、あらゆるものが高い。飛行機の外装板成形は「一回で必ず成功させる」という一発必中の姿勢で取り組む必要があるのです。
航空機の胴体で使用される外装板部品は、リージョナルジェットクラスで約100種類もあること考慮すると、生産工法の効率化は必須の要件となります。
そこで、コンピュータ内でパラメータを変えながら試行錯誤を行う、つまり成形シミュレーションを活用することで、コストを抑えて生産の効率化をはかろうということになりました。
私たちは、2010年ころから解析ソフトによる成形シミュレーションを活用した改善に取り組みを開始しました。その後、2015年からイーエスアイのPAM-STAMPに切り替えました。
PAM-STAMPに切り替えた理由
― 切り替えに至った経緯はなんでしょうか。
ポイントは、ツールとしての「効率性」と「操作性」でした。
それまでは、解析に必要なパラメータを設定するだけでも多くの時間を要していました。また、航空機は、多品種・少量生産であり、解析の他に一人で設計・製造・計測等幅広い業務をこなさなければならず、一業務のために多くの時間をかけることはできません。
このような背景があり、作業の効率化を期待して、2014年頃から解析ソフトの切り替えを検討しはじめました。各種ソフトウエアのベンチマークを実施し、我々の作業に最も適した日本イーエスアイのPAM-STAMPを採用しました。
PAM-STAMPへの評価
― これまでPAM-STAMPを使ってみての評価をお聞かせください。
作業性については劇的に改善されました。
以前は解析条件の設定作業に苦労していたスタッフも、PAM-STAMPはラクに使いこなしています。例えば、「マクロ機能やメッシュ自動修正機能等によって、作業が効率化されました。以前は、解析条件の設定作業に一週間かかっていましたが、今は1時間足らずで行えるようになりました。
PAM-STAMPの導入により作業時間が大幅に短縮されました。つまり、「誰でも、早く、簡単に解析できるようになった」ということです。
PAM-STAMPのシミュレーション精度
― シミュレーションの精度についてはいかがですか。
シミュレーションの精度も大きく改善されました。実計測データとの比較を下図に示します。
実部品(3次元形状測定結果) PAM-STAMP解析結果
![]() |
![]() |
実計測とPAM-STAMPでのシミュレーション結果の比較
また、導入当初は使いやすさを重視していましたが、実際には、作業性だけでなく性能も向上していることが分かりました。
つまりPAM-STAMPは、「使いやすく、かつ解析精度も優秀だった」ということになります。
50%のコストダウン効果
― PAM-STAMPの導入効果を教えてください。
使用開始から7カ月で、すでに50%のコストダウンが実現しています。このコストダウンは、事前の成形シミュレーション適用によるスプリングバック対策精度が向上し、金型製作後の改修費用が低減したことが大きく寄与しています。
PAM-STAMPの有効性、コストダウンへの貢献はすでに明確になりました。今後はストリンガーやフレームなど他の構造体、そしてチタン部品の熱間プレス成形など他の部品、製法にもPAM-STAMPによるシミュレーションを積極的に導入していく方針です。対象製品が増えるほど、コストダウンの効果も向上することが期待されます。
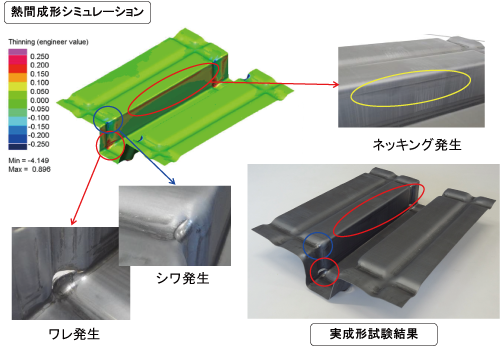
今後の期待
― 日本イーエスアイへの今後の期待をお聞かせください。
三菱重工 民間機事業部では、今後ともさらに高品質の航空機部品を開発・製造していく所存です。日本イーエスアイには、三菱重工の品質向上への取り組みを優れた製品とサポートを通じて後方支援していただくことを期待いたします。今後ともよろしくお願いします。
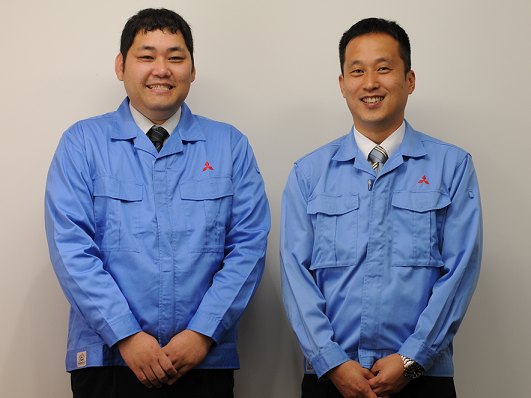
藤井 和慶氏(右)・土下 晋平氏(左)