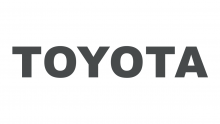
Toyota’s TILT Lab: Ahead of Its Time in a World of Digitalization
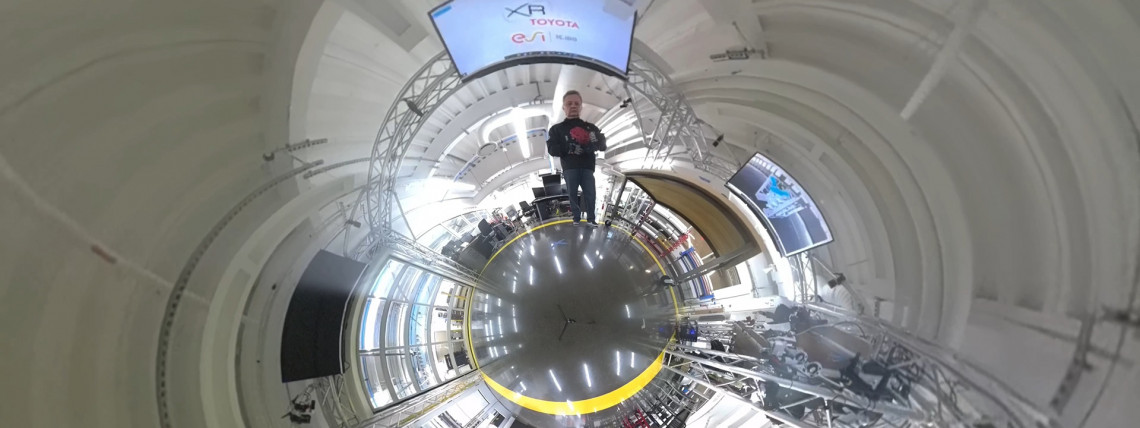
The future is so exciting with the transition to a mobility company, maturing mixed reality capabilities, technology options, and innovation. But even the best solutions or products are nothing without the people that have the vision, skill, and time to make them happen or function at the highest levels. ESI – from Sales, Support, Events, and Inclusion – has proven they have those values to support Toyota in providing its team members with the tools to build ever-better mobility for our customers in a more sustainable way.
Mark KuzniarskiAnalyst, Digital Intelligent Manufacturing Engineering/Toyota
For years, there has been a shift towards digitalization in the manufacturing engineering world. Manufacturers seek new ways to improve processes and produce a better product – it’s all about innovative solutions that disrupt and improve the traditional way of doing things.
Without a shadow of a doubt, the recent pandemic quickly turned that enthusiastic shift into a necessity. Thrust into a ‘digital-first’ world, manufacturers found themselves face-to-face with opportunities to reevaluate existing processes for improvement. Luckily for Toyota, they realized – pre-pandemic – that they needed to investigate solutions that could reduce the high cost and long lead times of physical prototypes where possible. The TILT Lab made it a mission to aggressively transform toward Industry 4.0 and a world of high-fidelity virtual prototypes; when the pandemic hit, they were ready. Their specific needs centered around validation related to product integration and manufacturing process – do the parts fit like they’re supposed to, and can we build the product as we imagined? The TILT Lab is a significant piece to the success of this evolution.
Toyota created the lab to be a place where “team members are encouraged to ‘tilt’ their conventional thinking on its axis and help them see concepts through to prototypes”. The team has everything from 3D printers to virtual and augmented reality technology, and lasers at their fingertips. The Lab encourages teams to bring their wildest ideas to life! Once proven, TILT Lab creations may be applied at Toyota plants to improve processes or solve challenges. Keeping with one of Toyota’s core principles of Kaizen – a quest for continuous improvement; Mark has contributed to the TILT Lab by implementing 3D printing, Augmented Reality, and Virtual Reality. He discovered that combining these technologies could identify and resolve issues with one voice months earlier by blurring the lines between design, engineering, and manufacturing by working together at every phase.
Mark, can you tell us what makes the TILT lab great?
The TILT Lab is a restriction-free sandbox allowing any idea, utilizing any software and/or technology to quickly flow through its Proof-of-Concept process, increasing team members’ skills and innovation with the overarching idea that digitalization helps achieve sustainability
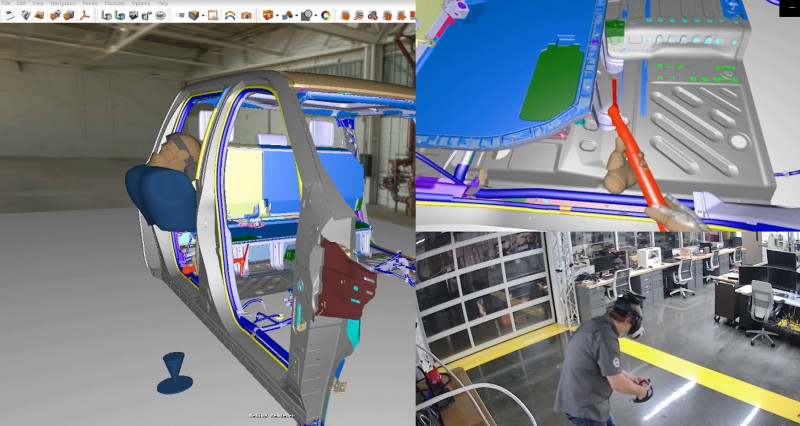
A mission zero partner Toyota can depend on
At Toyota, the expectation is that kaizen is not complete until yokoten (meaning ‘horizontal deployment’) is confirmed and the learning is shared with others. Equipped with ESI’s virtual prototyping capabilities, specifically using virtual reality (VR) to conduct immersive product reviews or experience virtual assembly processes, Toyota accelerated their already avant-garde approaches by sharing the results with Toyota Motor Corporation, R&D in Michigan, and Manufacturing facilities across North America. The main outcome is the inclusion of Design, Engineering, and Manufacturing early in the design phases gives Toyota the confidence to validate processes for new products with physically reliable scaled virtual versions of engineering accurate data, whether for process validations or design reviews.
This new approach led to a domino effect of additional benefits. With Cooperate or remote collaboration capabilities, Toyota can now connect their activities to a central location, like the TILT lab, with their distributed teams, working without interruption through unforeseen travel restrictions or supply-chain disruptions. At the same time, it also allows them to conduct, virtually, the physical assessments that were historically the cause of high cost and long lead times. Even now as travel restrictions are lifting, with the reliability and accuracy VR capabilities and virtual collaboration provide, Toyota has continued to significantly reduce employee travel, leading to a reduction in their carbon footprint. Last but certainly not least, teams are finding an even better work-life balance.
Toyota and ESI continue to ‘TILT’ towards the future together
As part of Toyota’s continuous digital transformation, virtual prototyping has allowed them to innovate safely and quickly, delivering the highest-quality products to market while consuming fewer resources than ever before. When we asked Mark Kuzniarski, an analyst for the Digital Intelligent Manufacturing Engineering Group at Toyota, what the biggest benefit of employing virtual prototyping has been, he said: “The future is so exciting with the transition to a mobility company, maturing mixed reality capabilities, technology options, and innovation. But even the best solutions or products are nothing without the people that have the vision, skill, and time to make them happen or function at the highest levels. ESI – from Sales, Support, Events, and Inclusion – has proven they have those values to support Toyota in providing its team members with the tools to build ever-better mobility for our customers in a more sustainable way".
We can’t wait to see what comes next, Toyota!